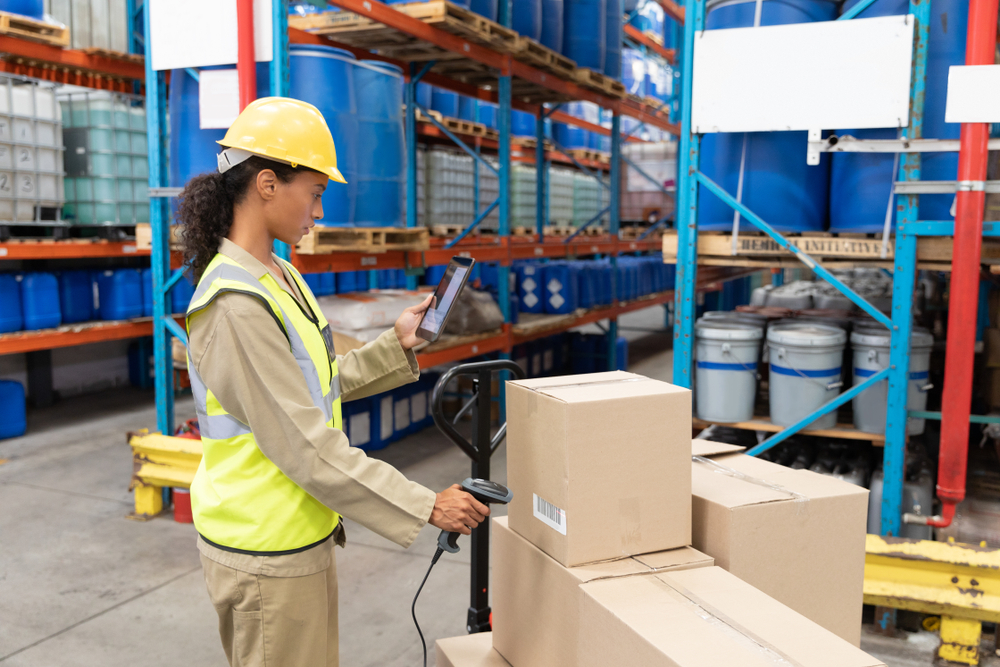
Many warehouse managers and business owners view safety supplies as an unnecessary expense, failing to recognize that the cost of workplace accidents can be significantly higher than the investment in proper safety equipment. From medical expenses to legal fees, productivity losses, and reputational damage, a single accident can have far-reaching financial consequences. In warehouses across Bryan Ohio and beyond, businesses that fail to prioritize safety often find themselves struggling with unforeseen costs that impact their bottom line.
One of the most critical aspects of cost-effective warehouse safety is understanding the direct and indirect costs of accidents. Direct costs include medical bills, worker’s compensation, and regulatory fines, while indirect costs—often more substantial—include loss of productivity, equipment damage, increased insurance premiums, and the challenge of replacing injured workers. By implementing proper safety measures and investing in high-quality warehouse safety supplies, businesses can drastically reduce workplace accidents and protect both their employees and financial stability.
How Safety Equipment Reduces Workplace Accidents
Warehouses are inherently hazardous environments, filled with heavy machinery, high shelving, and a constant flow of materials. Slips, trips, falls, and equipment-related injuries are among the most common causes of workplace accidents. However, these risks can be mitigated with the proper use of safety supplies. Items such as high-visibility clothing, hard hats, protective gloves, and slip-resistant footwear are essential for ensuring that workers are safeguarded from potential hazards.
Beyond personal protective equipment (PPE), warehouses in Bryan Ohio and across the country have embraced additional safety tools to create a safer work environment. Protective barriers, anti-slip mats, ergonomic lifting devices, and emergency eye-wash stations all contribute to reducing injuries and increasing efficiency. Signage that clearly marks hazardous areas and the proper use of lockout/tagout (LOTO) procedures prevent machine-related injuries. With comprehensive safety protocols in place, companies can significantly reduce workplace accidents, leading to fewer injury claims and less downtime.
Preventing Downtime and Maintaining Productivity
In any warehouse, downtime is a costly issue that directly impacts profitability. Whether it results from a workplace accident, an equipment malfunction, or non-compliance with safety regulations, any halt in operations can lead to missed deadlines and dissatisfied customers. Investing in cost-effective warehouse safety solutions helps mitigate these risks by keeping workers healthy and ensuring machinery functions smoothly without unexpected interruptions.
One of the most substantial ways to prevent downtime is through regular maintenance and the use of safety-focused equipment. Properly maintained machinery and ergonomic solutions reduce strain-related injuries, allowing workers to perform their tasks efficiently. Additionally, warehouses that prioritize safety tend to experience higher employee morale, leading to increased motivation and productivity. Workers who feel protected and valued are more likely to perform their jobs with focus and precision, reducing errors and improving overall workflow.
For warehouses in Bryan Ohio, local regulations and industry standards require compliance with specific safety measures. Failure to meet these requirements can lead to costly fines and potential shutdowns. By proactively investing in safety supplies and compliance tools, businesses can ensure they remain operational without costly delays or legal complications.
The Long-Term Financial Benefits of Safety Investments
While some businesses may hesitate to allocate funds toward safety supplies, the long-term financial benefits far outweigh the initial investment. A well-implemented safety program leads to lower insurance premiums, reduced worker compensation claims, and decreased employee turnover. When employees witness their company’s commitment to their well-being, they are more likely to remain loyal and engaged, saving businesses from the high costs associated with recruitment and training new staff.
Furthermore, a safe work environment leads to improved operational efficiency. Employees who have access to the right safety equipment can complete their tasks faster and more effectively. Reducing workplace accidents also means less money spent on injury-related expenses and legal battles, allowing businesses to reinvest their funds into growth and expansion.
Warehouses that emphasize cost-effective warehouse safety also gain a competitive advantage. Clients and business partners prefer to work with companies that prioritize compliance and efficiency. A strong safety record can enhance a company’s reputation, attracting more business opportunities and making it easier to secure contracts with larger corporations that have strict safety requirements. In the long run, businesses that invest in safety supplies and procedures will experience not only financial stability but also a stronger market presence.
Implementing a Safety-First Culture in Warehousing
Creating a culture that prioritizes safety requires more than just purchasing equipment—it involves comprehensive training, clear communication, and continuous improvement. Employees must be educated on the correct usage of safety gear and the importance of following safety protocols. Regular safety drills and refresher courses ensure that workers remain vigilant and aware of potential hazards.
Management plays a crucial role in fostering a safety-first culture. Encouraging open communication between employees and supervisors about safety concerns creates an environment where workers feel comfortable reporting potential risks. Addressing these concerns promptly prevents minor issues from escalating into major accidents.
For warehouses in Bryan Ohio, partnering with local safety organizations and staying updated with OSHA regulations is an excellent way to maintain compliance and ensure best practices. Investing in high-quality safety equipment, conducting regular risk assessments, and reinforcing safety protocols contribute to a work environment where accidents are minimized, and productivity thrives.
Conclusion
By taking a proactive approach to warehouse safety, businesses can avoid costly accidents, maintain seamless operations, and boost overall profitability. Whether through protective gear, ergonomic solutions, or ongoing training, the benefits of investing in workplace safety far exceed the costs, making it a critical component of long-term success in the warehousing industry.
Need Packaging Supplies in Bryan, OH?
Lamberson Packaging Solutions is a family-owned business that has been serving the greater Bryan, Ohio area for 15 years. We offer our customers the best product selection, fast delivery and do it all at great prices! We are proud to offer over 18,000 quality products from well known and trusted brands like 3M, Sealed Air, Tape Logic, Rubbermaid, Ivex, and many more! Our mission is to be the single-source answer to all of our customer’s packaging needs. Through the years, we have established a reputation with our customers for providing fast, reliable, and professional service. Our high level of responsiveness to our customer’s needs keeps them coming back! Give us a call today to get started!